
Common Causes of VFD Failure
Keeping Your VFD Maintained
The first thing you should know when purchasing a VFD is to keep it clean, cool, and dry. If you follow these three recommendations, the life of your VFD will be greatly extended. Unfortunately, there will come a time when your VFD will encounter a problem (hopefully many years down the road). This article will cover some of the most common causes of VFD faults and failures and provide some tips and tricks to prevent them to keep your equipment in tip-top shape.
Poor Environment
VFDs are built like computers, and computers are extremely susceptible to dust, debris, moisture, and overheating. If you are using a VFD in an area that is consistently taking in dust, debris, or moisture the operating life of your VFD will be shortened.
In environments with high humidity, such as wastewater treatment plants, your VFD is at risk for circuit board corrosion from moisture being sucked into the cabinet through the cooling vents constantly. This, compounded by possible infrequent use, can enable moisture to build up without time for heat and ventilation to dry it out. To avoid issues caused by humidity, ensure that the operating environment and storage space for your VFD is clean and dry, and consider a dehumidifier to dry out the air (ensure the dehumidifier does not leak near any electronic equipment). For extreme humidity or wash-down environments a NEMA 4, 4X or 5 enclosures may be necessary.
Another common cause of VFD failure due to environment is the clogging of cooling vents by airborne particles, especially when combined with moisture or oil. Metallic particles can also short circuit your VFD circuit boards. Tracking or arcing marks across components or circuit board traces indicate evidence of contamination failure.
To combat negative side effects or possible catastrophic failure due to build up, clean all parts of your VFD at least monthly. Also make sure you are using the correct cabinet for your environment. Some cabinets have side vents for cooling airflow, but these are more open to contamination. You are able to purchase drives in a sealed, dust-free housing if needed. Remember: Keep your VFDs free from dust, debris, and moisture at all times.
Loose Connections
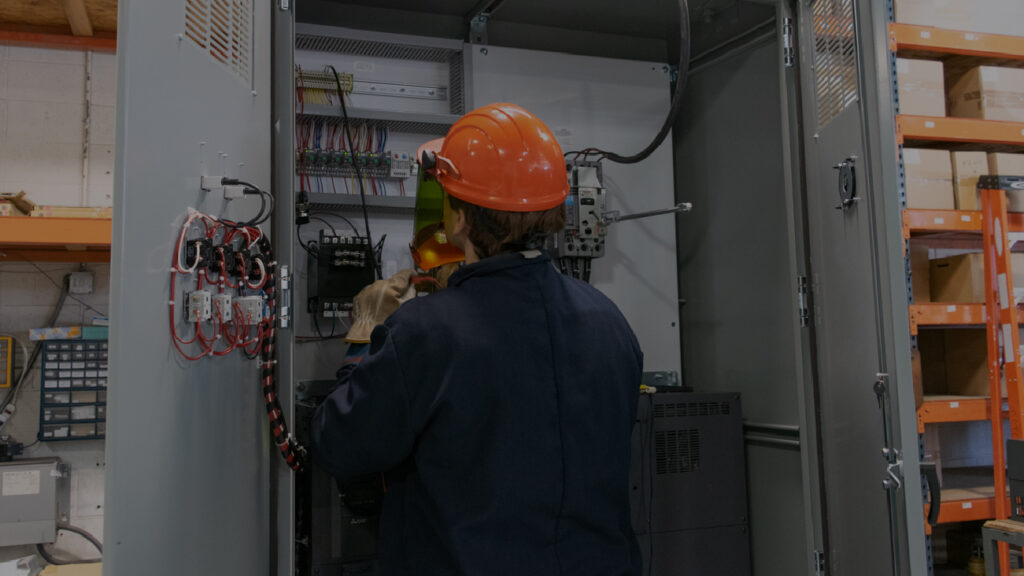
If you feel like your VFD is not performing quite like it used to, loose connections or aging components could be the culprit. High levels of vibration and heat production are the two main causes of loose connections and premature aging of certain components. This can lead to dangerous electrical arcing within the circuitry. Arcing can cause issues with other parts of your equipment and create a dangerous working environment for your employees or technicians. Loose connections can cause permanent damage to your equipment if not addressed as soon as possible.
Excess heat, usually caused by contamination buildup, can also occur when current exceeds the drives rated level or by loose connections. Checking the connections visually may not be enough to diagnose a loose connection; you may need to use a temperature probe or handheld digital pyrometer. Connections should never be hotter than the connecting wires; this is a sign of a loose connection. Overheating can cause blown capacitors, shorting, and excess wear on many different components.
Wrong Equipment
Unfortunately, you may be recommended the wrong VFD for your equipment. If you accidentally connect your VFD to an incompatible motor or machine, performance degradation is inevitable. Always make sure you double or triple check the compatibility of your motors/machines before you connect your VFD to the device.
Overuse
Using VFDs beyond their manufacturer’s recommended operating limits (by choice or on accident) can contribute to failure. Using any component at a rating higher than its operating limit decreases the lifespan of said component and eventually leads to failure. To avoid issues due to overuse check that all inverters are being run within manufacturer’s recommendations.
High Bus Fault
This is a common fault that is caused by external factors. An instantaneous voltage spike in the ac line or an “overhauling load” created by the inertia of the machine is usually the cause a high bus fault. This happens when the load continues to rotate faster than the motor’s commanded speed. Usually when this happens, the VFD protects itself by tripping on a high bus fault and shutting off the IGBTs.
If your VFD indicates a high bus fault, ensure that the power supply is consistent and that the deceleration time is adjusted to match the load. If the process requires rapid deceleration, dynamic braking or a regenerative power control circuit may be added to assist the VFD and prevent a high bus fault.
Overcurrent Fault
This is another common fault usually caused by too-fast acceleration at start-up. To ensure you don’t have an overcurrent fault, check all power connections to ensure that they are properly attached. Loose power connections cause overvoltage or overcurrent, blown fuses, and inevitably VFD damage. Loose wiring can cause erratic drive performance. This can result in unpredictable speed fluctuations and an inability to control your VFD.
To help prevent overcurrent fault use an auto tuning feature (if your VFD offers it). This function enables the drive to identify the attached motor. This allows rotor information to be used in processor algorithms for more accurate control.
The second way to prevent overcurrent fault is to check the mechanical load for worn or broken parts, or excessive friction. Repair or replace any worn or broken components as needed.
The last way is to check incoming voltage and acceleration rate. If incoming voltage is too low, or the acceleration rate is set too fast, overcurrent fault is possible. Stabilize the incoming voltage and acceleration rate to correct the fault.
High Starting-Load Current
A high current or high load reading could possibly indicate mechanical binding or some unexplained changes in process speed or load. The power requirements for pumps and fans ran even just a few revolutions per minute faster than normal can overload a VFD.
Make it a point to inspect all components driven by the VFD before starting them up. Conveyors must be unloaded before startup, pumps should be cleared of all debris or ice, and moisture should be avoided on any load. Wet material is much heavier than dry material and can place an unexpected load on the VFD, this can cause motor or VFD overload.
Another way to reduce a high starting load is to use a VFD with an extended acceleration rate. This starts a load slowly and smoothly instead of jerking to a start. A slow, smooth start is easier on mechanical components and has lower line requirements because a VFD draws only 100-150% of the load.
Capacitor Fault
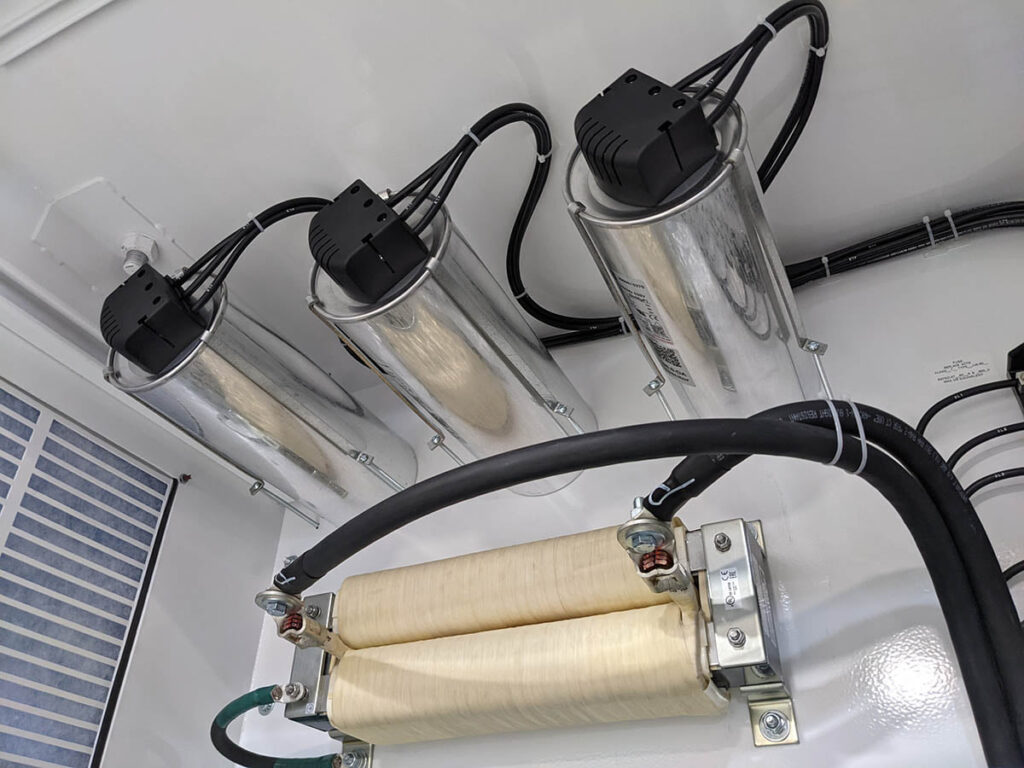
Electro-mechanical wear happens to electrolytic capacitors since they have a limited lifespan and age faster than other components. This in itself could be a cause of inverter failure.
Capacitors are also extremely temperature sensitive. Operating temperatures over the manufacturer’s recommendations (often caused by high current) will reduce the life of the components. Electrolytes evaporate faster at higher temperatures. Capacitor life increases when they are consistently used at lower than operating temperature.
Useful Questions to Ask for Diagnosis
When helping your VFD technician to troubleshoot your VFD, you should be prepared with the answers to these questions:
- What was the machine driving at the time of failure?
- Did the machine jam for any reason?
- Did any other devices trip at the same time as the VFD?
- Are there any power factor correction capacitors on site? If so, when are they switched?
- What was happening on the utility side?
- Did the utility observe any disturbances?
- Was there an electrical shutdown caused by lightning or brown outs?
- Was there any construction or welding going on near the VFD?